Optimizing Supply Chain Performance and Customer Satisfaction: Using Statistical Forecasting and an Innovative Configure-to-Order Process to Improve Critical Operational Metrics |
By Michael A. Massetti, Corporate Vice President, Integrated Supply Chain at Advanced Micro Devices, Inc.
A supply chain’s focus on customer service levels has enabled business growth but challenges the desire to maximize working capital and asset utilization in factories. AMD supports supply flexibility for customer satisfaction while striving for best-in-class demand and supply planning practices. The Central Demand Planning (CDP) and the Supply Chain (SC) teams worked together to improve forecast accuracy by building a statistical model which categorizes the risk of building product ahead of orders. In addition to categorizing risk, the SC team implemented a postponement step in the test cycle to strategically position low risk product. When orders are placed late in the cycle or within lead-time, AMD can fulfill the orders quickly with minimal impact to its production efficiency.
Situation
Today’s global marketplace and volatile economic conditions make it essential for supply chain organizations to develop and execute strategies that optimize company costs while delivering differentiated value to customers.
AMD strives to optimize its “triangle of metrics” -- delivery performance to customers, inventory optimization to maximize cash, and forecast accuracy. Many dependencies and factors relate all three points of this triangle of metrics into a unified supply chain. Here we focus on two elements of this essential model: how to improve forecast accuracy and how to use manufacturing postponement to reduce and optimize inventory while maintaining and improving service levels to customers. The first relates to introducing a statistical model to better predict what products will be requested to ship and billed during the quarter. The second is a new concept called “Finished and Unmarked,” or FUM.
Breakthrough Leadership
Beginning in Q1 2010, CDP built and back-tested the intra-quarter statistical model (IQSM) for two quarters for all microprocessor products. In Q2 2010, Supply Chain began testing the configure-to-order (CTO) process. In the second half of 2010, both initiatives became operational. CDP analyzed the demand plan versus available capacity to establish the amount of inventory to be postponed at a point in the test process called FUM for later completion. Depending on capacity, production levels were set at agreed-to linearity levels with the factory. If capacity was heavily utilized, a higher amount of finished goods were produced to avoid shortages at quarter’s end.
Solution
IQSM projects likely end-of-quarter billings with a 95% confidence interval based on historical billings linearity. This capability exists by product line, by product family, and by customer. In addition when compared with the sales forecast and backlog, IQSM identifies risks and opportunities. To optimize inventory, it is critical to understand and manage the demand plan relative to the likely quarterly billings outcome. This allows demand planners and the supply chain to correctly position inventory at the right point to meet sales while not building up finished goods. This helps avoid growth of aged or obsolete material. In addition, understanding this relationship allows both teams to monitor capacity and make decisions about factory utilization should the expected outcome of the quarter changes.
On a weekly basis, demand planners and the supply chain team review an analysis comparing IQSM, sales forecast, B+B, and current ship plan at various levels of detail. The following questions are answered:
- What are the likely quarterly billings versus forecast and budget plan?
- What risks & opportunities exist?
- Should we change the plan (volume and mix) to minimize finished goods inventory? What is the likely resulting ending inventory if we do not change?
- What capacity do we have if upsides to demand occur?
To run an efficient factory a linear production plan throughout the quarter is ideal. Often billings are back-end loaded. It is not cost effective to build capacity to map production toa skewed loading. That is, capacity required to meet the late demand surge would be completely under-utilized during the first part of the quarter. The challenge, given back-end loaded billings and the flexibility to respond to changes in demand, is the need to build product in the beginning of the quarter to linearize factory utilization. IQSM also helps characterize and sequence risk of the likely quarterly billings, helping the supply chain determine which products should be builtin which sequence. In the next section, FUM will be explained in detail, which is how the supply chain utilizes IQSM to preposition the appropriate product.
FUM is apostponement point after test and before final marking in the manufacturing process, which differentiates a highly similar parts into distinct product SKUs. Since implementing FUM, AMD has reduced factory variation by 50 percent, contributing to supply chain agility, lower costs, and more optimal inventory. FUM is a configure-to-order strategy that reduces dependency on forecast accuracy of product mix and improves support of upside demand inside lead-time. This allows AMD’s factories to operate build-to-forecast, build-to-order, and configure-to-order processes concurrently. Supply chain segments production based on standard ABC volume classification and by using the IQSM output to validate the plans.
Postponing production at FUM delays building AMD’s inventory of microprocessors until an order is received. The manufacturing flow is the point at which AMD differentiates microprocessors into the SKUs that consumers order. At FUM there are options to create four or more unique SKUs from a single postponed part. This adds significant flexibility to AMD’s inventory and enables efficient satisfaction of constantly changing customer demands.
Holding the material at FUM provides the flexibility of waiting to select the final SKU until customers demand it.
- First, material that would have normally been differentiated and finalized based on a market forecast is now held at FUM until an order is received.
- Second, to improve factory linearity, extra material is inserted into the back-end production flow during low points and processed up to FUM to await marking based on actual or predicted orders.
High customer demand drains the accumulated FUM. By holding material — instead of finished goods — in FUM, AMD’s supply chain reduces finished goods inventory while still responding to demand changes. FUM allows AMD to simultaneously optimize materials inventory and maximize market responsiveness without pushing factories into overtime.
The decision to delay material prior to shipment at FUM is a postponement tool to help balance three metrics: finished goods inventory, forecast mix accuracy, and factory loading.
Outcomes
Results show significant improvements in factory linearity and finished goods inventory levels. Within a three quarter period, inventory of finished goods have declined by 32%. Overall, it is the direct result of predicting the likely end-of-quarter billings more accurately and managing the demand plan accordingly. Factory linearity variance has been reduced 50%. By prepositioning the correct WIP, which can be finished into several products through FUM, AMD is better able to manage factory linearity even though it must build product well ahead of billings.
A robust supply chain must respond to shifts in customer demand. AMD has worked aggressively to meet changing demand while operating a cost-efficient and high-performing supply chain. The key is to do it profitably and in a way that optimizes working capital. Through IQSM and FUM processes, AMD is demonstrating that it can achieve both goals.
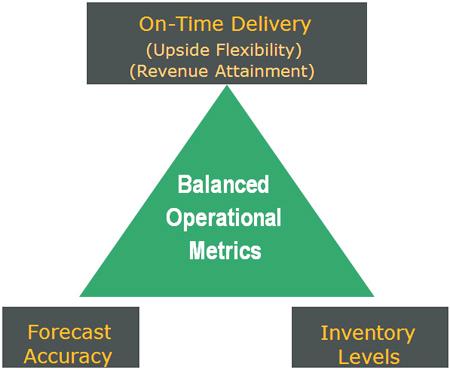
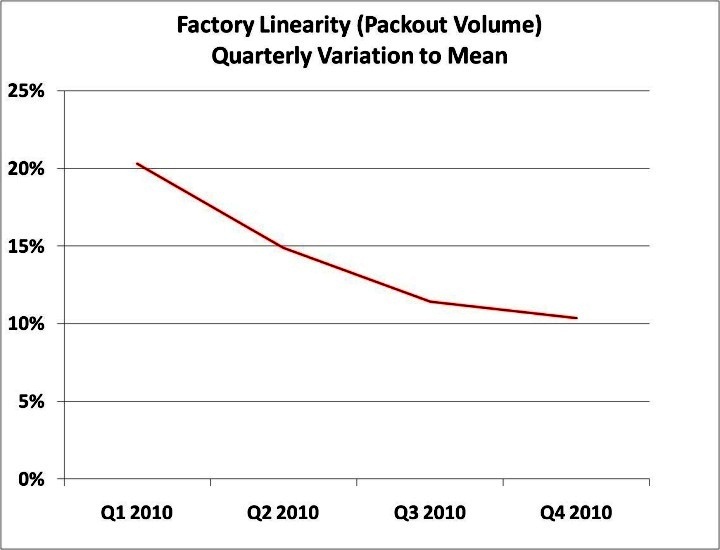
|
About the Author: |
Michael A. Massetti is Corporate Vice President, Integrated Supply Chain at Advanced Micro Devices, Inc. In September 2011, Mr. Massetti was awarded Supply Chain Executive of the Year by The Global Supply Chain Leaders Group (GSCLG). The award is presented to the individual who received the highest aggregate ratings in making significant contributions to the advancement of the Supply Chain Management profession and maintaining sustainable, responsible business practices in its global operations during the past year. |
|
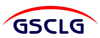 |
|
November 2011 |
|
|
|
|
|
|