Just-in-Time to Just-in-Case
Reprinted by permission from the Graziadio Business Report, Vol. 6, Iss. 3, 2003
http://gbr.pepperdine.edu/032/supplychain.html |
Managing a supply chain in uncertain times
Charla Griffy-Brown, PhD
In the current uncertain political and economic environment, companies need to adapt their supply
chain to deal with uncertainty.
Developing better ways of dealing with supply chain disruptions is particularly important since
sustainable competitive advantage is often driven by speed, delivery and cost-reduction. Whether
intentional or due to natural catastrophe, these disruptions for businesses usually go straight to the
bottom line.
What makes disasters and the resulting business disruptions particularly significant today is the
emphasis on speed and efficiency. This is generally epitomized in the Just-in-Time system of delivery
of materials and components that was pioneered by Japanese manufacturing firms. This technique
requires inventory to arrive at the production lines precisely when it is needed. In the 1980s, a few U.S.d
manufacturing firms took their cue from their Japanese competitors and began to cut the slack and
related waste out of their own supply-chain networks. As a result, Just-in-Time concepts have now
been widely adopted across both traditional and high-tech industries in the United States and Europe.
The inventories of both raw materials and finished goods have been dramatically reduced for these
organizations, thus making capital available for more profitable uses.
However, shortages caused by natural, political or technological disruptions can erode productivity and
even bring business to a halt, thereby causing customers to defect, never to return. The potential for
supply-chain disruptions means business operations are less predictable than most managers believe.
In the current uncertain political and economic environment, companies need to adapt their supply
chain to deal with uncertainty.
The Evolution of Supply Chain Design
Existing supply chain technologies were primarily designed to reduce the friction in the flow of
materials, components, and finished goods across the enterprise and its global supply chain. When
these systems were introduced, the level of global uncertainty both politically and economically was not
the consideration it is today. However, recent corporate experience with some natural disasters and
other disruptions has made it clear that there could be significant risks in this regard. Beyond these
experiences, the catastrophe of September 11, 2001, and the continuing threat of deliberate disruption
have also changed the environment.
Where Do U.S. Firms Stand Now?
According to recent research, firms are not prepared to manage the risks that could hit their supply chain in the event of a local, national or global crisis. A forthcoming study by the Council of Logistics
Management notes that approximately 60% of the firms queried acknowledged that they had formal
continuity planning programs in place prior to 9/11 and that this number did not change significantly
after this event. Though 9/11 is statistically an outlier in terms of probability of disruption, events of this
magnitude should serve as a wake-up call. Preliminary findings from the study suggest the even the
existing formal continuity plans do not cover the full supply chain or even enterprise supply chain
resources. Additional surveys by the Chartered Management Institute and the Business Continuity
Institute show that there is evidence of significant disruption to organizations from a number of crises in
the late 1990s through 2002. Furthermore, according to this survey data, there seems to be an
escalation in the number of disruptions, but little change in contingency planning.
Lessons from the Previous Disruptions
How can business practitioners effectively deal with these risks and capitalize on the opportunities?
One way is to learn from company responses to previous catastrophic events. A brief comparison of
different firms' successful and unsuccessful responses to supply chain disruptions points to some
effective lessons for business practitioners. Table 2 outlines a brief comparison of some significant
events from the late 1990s to the present.
Table 2. Comparison of Disasters Resulting in Significant Supply Chain Distribution and Firm
Responses
Crisis |
Impact |
Management |
Hurricane Mitch in
Honduras, Guatemala
and Nicaragua
(November 1998) |
Flooding destroyed
banana plantations, thus
damaging 10% of the
worldwide crops. |
Chiquita: leveraged alternative source of
bananas to maintain deliveries.
Dole suffered revenue declines and struggled
to find alternative sources of supply. |
Earthquake in Taiwan
(September 1999) |
Power outages and
damaged equipment
halted supply of
components to PC
manufactures. |
Dell influenced demand toward products with
available components through direct sales
model.
Apple faced product backlogs due to
component shortages and inability to alter
product onfigurations. |
Outbreaks of mad cow
and foot and mouth
disease in England
(Spring 2001) |
Destructions of cattle
caused shortage of
European hides to leather
goods manufactures, |
Natale, Gucci and Wilson Leather were
locked into supply contractors; Naturalizer,
Danier and Justin Boot relied on inventories.
Etienne Aigner shifted purchases to other
regions, but faced stiff cost increases. |
Terrorist attacks on the
United States
(September 11, 2001) |
Increased security
crippled transportation
networks, thus causing
cross-border shipment
delays to US auto
manufacturers. |
DaimlerChrysler, Continental Teves used
alternate modes of transportation and
implemented contingency plans.
Ford was forced to close five plants for
several days. |
Source: mmc.com and Chartered Management Institute
Transportation: Examination of this comparison shows the importance of lining up alternative
transportation. While such a strategy may seem obvious, the examples of Diamler Chrysler versus
Ford indicate that unfortunately, even large, profitable companies may not have alternative
transportation strategies.
The attacks of September 11 immediately prompted tighter security at all U.S. customs checkpoints,
thereby causing significant delays at border crossings for several weeks and disrupting critical
shipments of parts and components. Ford suffered from not being prepared with alternate
transportation for critical components. Consequently, Ford had to shut down five of its U.S. plants
because the company could not get enough engines and drivetrain parts from Canada. Ford's
production for the fourth quarter was 13% fewer vehicles than planned as a result of these problems.
In contrast, Chrysler responded quickly to the restrictions on air travel after September 11. Chrysler's
logistics staff in Michigan had analyzed its production flow by September 12 and realized they were
likely to run out of an updated steering gear unit for the redesigned Ram pickup truck. The part was
usually sent by air from a TRW plant in Virginia to the Chrysler assembly plant in Mexico. Chrysler
turned to a truck service to minimize the delay in delivering the component.
Continental Teves, a large supplier to the auto industry, similarly demonstrated agile supply chain
management. Their crisis team, composed of purchasing and logistics managers, immediately put
together a list of all customers, parts, and suppliers outstanding. They identified where the parts came
from and assessed which were considered critical and vulnerable to delay. By the afternoon of
September 11, they knew which North American shipments required immediate action and expedited
many of these by land. Continental Teves used existing contingency relationships with transport firms
such as Emery to supplement air cargo delivery. Toyota, among other customers, benefited from
Continental Teves' ability to deliver with little disruption in the week that followed.
As these events make clear, manufacturers and suppliers must have the flexibility to expand their
contingent shipping arrangements. In this regard, logistics software can help by tracking goods globally
and providing guidance when disruptions occur. Those that ship via one mode of transportation should
consider backup routes by another mode. These steps may raise costs and affect production lead time,
but determining the balance between flexibility and extra cost is part of the new "just-in-case" equation.
Sourcing Alternatives: An examination of these comparisons reveals the importance of cultivating
alternate sourcing arrangements. Relying heavily on a single source for products or critical components
leaves a firm highly vulnerable to prolonged and expensive supply gaps. Again, this may seem like
common sense, but many firms have not considered enough alternative sourcing scenarios. The
Hurricane Mitch crisis is a good illustration.
Dole lost 70% of its 40,000 acres in Honduras, Guatemala, and Nicaragua -- roughly one-quarter of its
worldwide production. The company had no strategy in place for alternative sources of supply in the
region, and therefore suffered an interruption in supply from Central America that lasted more than a
year. As a result, Dole suffered a 4% decline in revenue for the fourth quarter of 1998 and lost over
$100 million dollars.
Chiquita Brands was able to maintain a steady supply of bananas even though it lost production from
its own Central America plantations. It met volume requirements through increased productivity in other
locations, such as Panama, and purchases of fruit from associate producers in the region that were
undamaged. Chiquita's revenues actually grew 4% in the fourth quarter of 1998.
Leveraging Technology: The evolution of the supply chain in recent years is characterized by a move
toward modularization and customer relationship management (CRM) integrated application suites.
Technology vendors were moving from tightly integrated inter-enterprise suites to modular applications
with a narrower focus. Modular applications with a narrower focus reduced implementation risks and
costs significantly. However, they also increased the potential customer pool for software companies by
bringing in small and medium-sized enterprises that were previously excluded due to the price of the
software.
The evolution of technology and customer relationship capabilities provides an opportunity for
managers to mitigate risks even in the worst of circumstances when supplies are just not available,
provided the supply chain system is contemporary and not too thin.
This new conceptual strategy for mitigating supply chain disruption is to influence customer choice.
Traditionally companies have created product lines that represent their best guesses about what
buyers will want. There were generally some alterations possible at the purchase point, but choices
were largely fixed. Customers were not used to variety or "mass customization," and companies could
not produce a high level of variety. Traditional vertically integrated operations, using a standard supply
chain, couldn't deliver custom products reliably or quickly. However, since the mid-1990s, more and
more companies have developed the ability to tailor in real time the options presented to the buyer and
to promote certain features over others through their digital networks.
This ability to dynamically influence customer choices is particularly powerful in times of crisis, as is
seen in the way Apple and Dell dealt with the Taiwan earthquake in 1999. This earthquake cut power,
damaged factory equipment and halted the supply of critical PC and laptop components for two weeks.
In this case, the problem could not be resolved with alternative forms of transportation or different
sources of supplies.
Apple faced shortages of semiconductors and other components that delayed production of its iBook
and Power Macintosh G4 desktop computers during a period of growing demand. The company was
unable to alter product configurations, but it decided to ship slower G4 comptuers than the customers
had ordered and received a barrage of complaints.
Dell on the other hand fared much better. Even though Dell's direct sales model meant that it held only
five days of inventory, Dell was able to continue selling and delivering product. Dell used price
incentives and promotions, adjusted in real time on Dell's online choiceboard, to influence customer
choice. Dell's third quarter 1999 earnings actually improved 41% over the previous year, despite the
supply-chain disruption.
Conclusion
Resilience in responding to customer demand is critical for surviving in a risky economy that demands
speed and flexibility. Many companies have spent decades trying to get their supply chains to flow
smoothly through just-in-time concepts. However, these ultra-lean strategies have significant risks in a
turbulent economic and political system. Each component in the supply chain, from sourcing to
inventory to transportation and demand management, must be reassessed based on the current
situation and careful consideration of risks. Furthermore, since these situations change so quickly, the
supply-chain system needs to be rebalanced periodically as new information and new risks are
identified. New ways of leveraging the information networks to mitigate risk represent a critical and new
component of business continuity planning. This means paying as much attention to demand
management and information sharing with internal and external customers as it does to logistics.
Building a flexible and responsive supply-chain service is a solid defense against inevitable
catastrophe and is critical amid the growing uncertainties in today's business environment. However,
the benefits are not just in risk-mitigation. This strategic approach incorporates competitive goals such
as anticipating and even influencing shifts in customer priorities and creating advantages over rivals
that are rigid in procurement, transportation and operations.
Large-scale disasters remind us that the frictionless economy is a just a dream, not a reality. No one
can predict where the inevitable next disaster will occur or what will happen. Mitigating risk entails a
high cost and sometimes constrains performance, so these things must be balanced. However,
businesses can succeed with agile supply chain management, particularly by leveraging customer
relationship management and other related technologies to influence customer choice. |
|
About the Author: |
Charla Griffy-Brown, Ph.D., an associate professor of Information Systems at Pepperdine University's Graziadio School of Business and Management, is currently part of an international research team
examining technology and development issues. Dr. Griffy-Brown graduated from Harvard University,
is a former Fulbright Scholar, and holds a Ph.D. in Technology Management from Griffith University in
Queensland, Australia. She has worked for NASA at the Kennedy Space Center and has taught
innovation/technology management courses in Australia, Singapore, Indonesia, Malaysia, and Japan. |
|
|
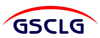 |
|
January 2009 |
|
|
|
|
|
|
|